

Since for quality processes, measurements at the end of the processes are vital, this can involve looking inside a microfluidic device. A requirement for quality process is analyzing specifications across a chip device, which, however, can be painstaking and time-consuming.Īs microfluidics channels often move more than just fluid and cells, the Z-axis dimensions can be quite significant, if they are in the millimetre range. Microfluidic devices have large XY geometry as they are as big as a glass slide, which in terms of microscopy, is deemed as quite large. Microfluidic device challenges for traditional quality microscopy methods, as shown on a cartoon representation of a microfluidics device cross-section. A method to examine a closed trench is also needed, as, after assembly, the finished device will also be subject to quality control.įigure 2 shows the three particular challenges that arise for quality methodologies employing conventional microscopy.įigure 2. Trenches may be up to hundreds of microns in-depth, so quality processes have to measure the distance as well as the depth of the trench. Microfluidic devices are three-dimensional in nature, which also possess challenges for techniques relying on probes. Microfluidic Device Challenges for Traditional Quality Microscopy Methods, as shown on a cartoon representation of a Micro fluidics Device cross-section. In addition, fast and specific quality control processes need to be developed to determine if a product conforms to the required specifications.įigure 1. These methods are not convenient to measure large dimensions in the XY directions as well as substrates measuring only in millimetres. For microfluidic devices, conventional quality methods using profiler probes or optical microscopy to validate the specifications are not successful (Figure 1). For optimizing the evolution from R&D to production, it is necessary to achieve the capability for measuring closed microfluidic devices on PDMS and glass. Hence, it is a big challenge to maintain similar geometries on PDMS. Moreover, R&D devices are usually glass-based devices, but mainstream fabricated devices use soft materials such as PDMS. Finding out the reason for the mismatch requires determining precise measurements of the fabricated device. It is almost impossible to match pre-production simulation with post-production performance. However, during device manufacture, precision is influenced by mating practices, surface treatments, surface roughness, and material spoilage caused during fabrication practices. Microfluidics operate on the basis of specific pressure points, flow dynamics and mixing streams, all of which need correct volume and flow simulations. Quality in Micro Fluidic Devices - A Challenge for Traditional Microscopy However, some manufacturing challenges remain for quality assurance, since the microfluidic device fabrication is often not connected with the end-users. According to, the global micro fluidics was estimated at US$3 billion in 2015.
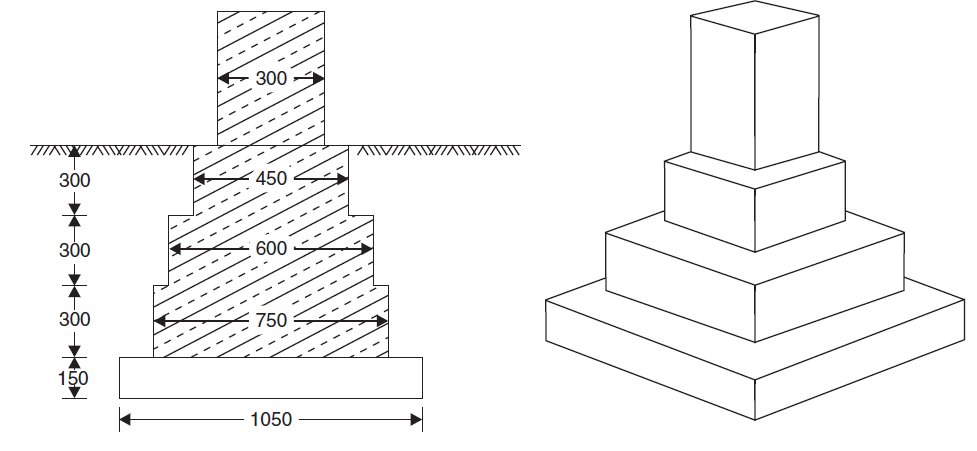
The words “Practical Microfluidics” found on the cover of the March 2014 issue of Nature reveal that microfluidics technology is becoming a mainstream technology.
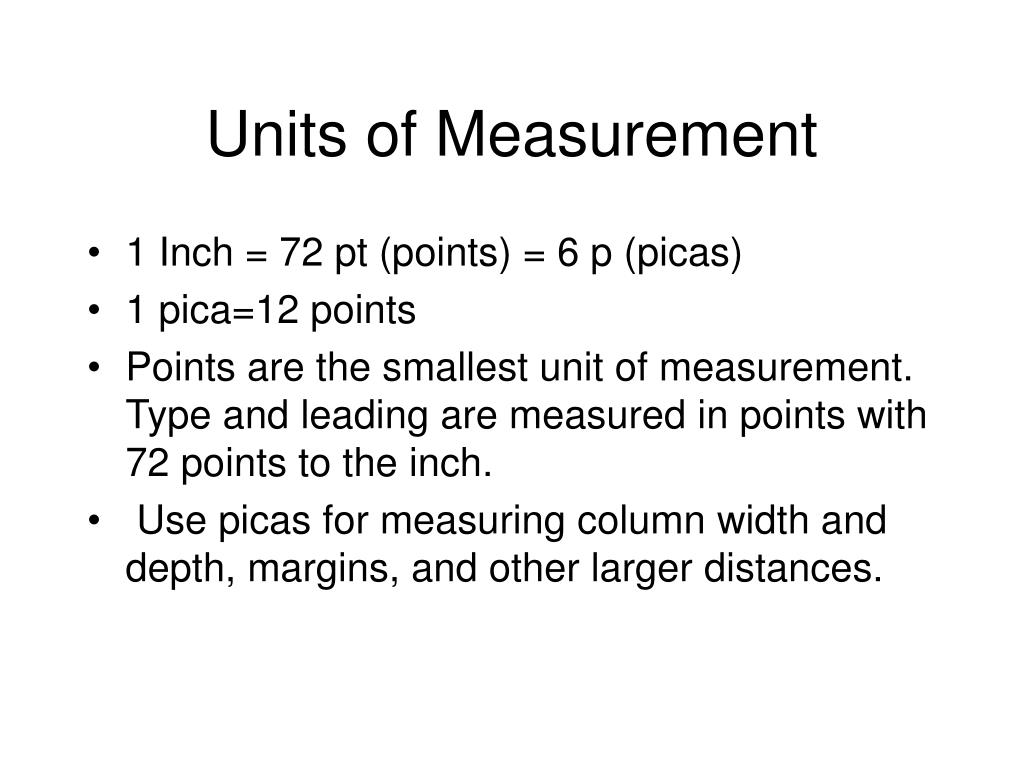
This article deals with the accurate and quick measurements of depth, flatness and width, of closed channel microfluidic devices, follwing fabrication.
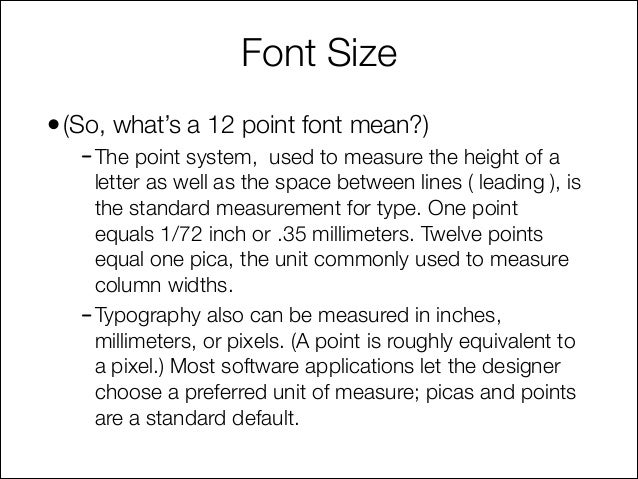
Sponsored by KLA Instruments™ Feb 15 2016
